Smarter sustainability: Engineering a more sustainable future
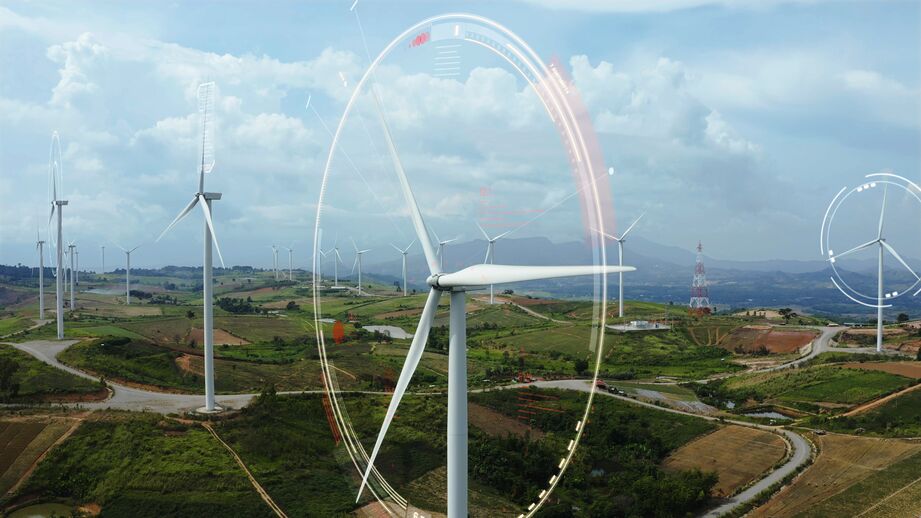
As leaders around the world last year made pledges at COP26 to take significant steps towards limiting the global temperature rise, it became clear an influential industry helping to achieve this target will be renewable energy. Solar photovoltaics, wind power, other renewable generation forms, and energy storage systems offer viable alternatives to fossil fuels, but they too have environmental, economic, and social impacts. Additionally, the industry faces tremendous cost pressures to make the mass adoption of renewables with storage commercially viable. For the manufacturing industry to ramp-up sustainable and efficient renewable energy, tremendous innovation and cutting-edge technology adoption needs to happen.
Hexagon is working closely with leading energy players to make the future of clean power generation more efficient. Here is a small overview of real-world examples showing how Hexagon’s digital twin simulations are put to work in the renewable energy industry to reduce material usage and number of physical prototypes, while improving product performance and sustainability.
Simulation solution for drivetrain miniaturisation
Here’s an example from ZF wind power. The wind market is facing critical challenges with costs, and one of the ways to reduce the cost of energy is by decreasing the amount of materials used and reducing the overall size of the turbine parts. For that reason, ZF is developing a power-dense, lightweight wind turbine drivetrain while they try to minimise the transmission error to reduce noise.
The key to a good simulation solution is to find the right level of model complexity. If it’s too simplified, you don’t get the accuracy you need, but if it’s more complex than is necessary, you’re also wasting time on modelling and computation.
In the original simplified drivetrain model, ZF engineers couldn’t match the physical testing results with the simulation results, and after adding another level of fidelity using Hexagon’s world-leading drivetrain simulation software, Romax, they found the perfect model to capture the centralised contact pattern on the gears in simulation. And once the correlation was achieved, they were able to perform an optimisation study to find the best gear topology to minimise transmission error and noise, saving a huge amount of time and cost on physical prototyping and testing. At the same time, the drivetrain was miniaturised to reduce material waste and the cost of energy production.
Blade lightweighting solution by structural analysis
Korea is vying to win the race to build the most sustainable cities, and that’s why the Korean government is heavily investing in renewable energy with its plans to build the world’s largest offshore wind power plant with the lowest cost of energy generation.
To reduce the weight and manufacturing cost of wind turbine blades, General Electric (GE) Co. and the National Renewable Energy Laboratory (NREL) have introduced a fabric-covered wind turbine blade design. The Korea Institute of Energy Research created a 10KW prototype to validate this new design.
To confirm that the structural integrity of this new design would be similar to typical wind turbine blades, structural analysis was carried out using Nastran, Hexagon’s structural analysis software, for the design loads. The wind turbine was simulated under multiple operating conditions including normal power production, grid shut down, emergency shut down and park, with the simulation results providing more than 90% correlation compared to the physical testing results, which is extremely good.
Hexagon’s material simulation software, Digimat, also captures the anisotropic material performance of composites, which is often used to construct the turbine blade. Having a realistic understanding of the material behaviour not only increases the simulation accuracy, but also helps engineers understand how to better recycle the materials after the turbine blades are decommissioned.
Solar tracker wind mitigation with simulation
In the solar energy industry, Hexagon’s engineering software has also been widely applied in companies like FTC Solar, a fast-growing global provider of solar tracker systems, to help engineers understand how strong gusts of wind and storm conditions can damage solar trackers. To simulate the solar tracking system’s mechanical performance, FTC Solar’s engineers utilised our multibody dynamics and structural analysis software to evaluate the possible dynamic structural stress scenarios during operation, especially under extreme loading conditions.
Building and running the smartest solar farm in the world
Not only has Hexagon been providing a full suite of industrial solutions and technologies to various OEMs and suppliers in the renewable energy industry, but we also started our own renewable energy project in April 2021 with the acquisition of a 40-hectare PV solar farm in Archidona, South West Spain near Malaga. The target is quite simple – to make the smartest solar project portfolio in the world with an ambition to deliver electricity at 30% higher project output than equivalent farms not using Hexagon’s technologies. Hexagon’s target efficiency improvements will cover everything from solar farm planning, design, manufacture, build, operation, and optimisation.
As an example, what has proven to be one of the most useful outcomes from this project is the connection of Cradle CFD to our Hexagon Xalt technology to produce an augmented reality visualisation of the facility onsite for operators to look at fluid flow effects and temperature as they hold their iPads or iPhones up and view what is in front of them on a given day.
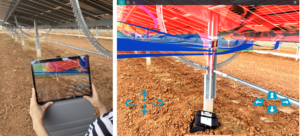
Figure 5: Hexagon’s CFD Digital Twin flow prediction at Hexagon’s Archidona Solar Farm in Xalt Augmented Reality iPad viewer
Conclusion
Hexagon is uniquely positioned to deliver software and hardware solutions across a broad array of sustainability applications. Our sustainability mission is entirely focused on putting virtual and real data to work in smart ways to increase efficiency, productivity, and quality in renewable energy facilities. In doing so, we mitigate the urgent risks of natural resource depletion and waste.
Contact us today to discover more about our sustainable solutions and how they can transform your industry.
Co-author: Yijun Fan – Director of Business Solutions Marketing, Hexagon Manufacturing Intelligence
For quality that touches peoples lives
Hexagon’s Manufacturing Intelligence blog is your go-to source for the latest manufacturing thinking. From expert commentary to industry perspectives, it’s designed to empower leaders and professionals to make smarter decisions, drive innovation and turn ideas into impact.