Remanufacturing Intelligence
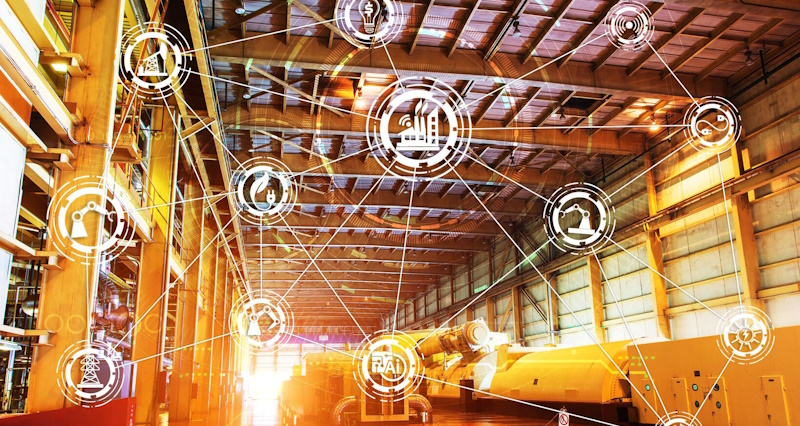
What happens to your products when they reach the end of their useful life? It’s a question that should be front of mind, yet according to the latest research, just 7.2 % of materials are cycled back into the global economy. In this blog I explore the idea of remanufacturing and deliver a vision for the future of manufacturing.
Imagine a product that goes through its useful life periodically “checking in” with its original manufacturer. It might tell you all sorts of useful things, like how it’s being used and what sort of environment it’s in. It could give you a report on each individual component. That information would certainly help us to design and build products that last longer and better satisfy customer requirements.
But it would also facilitate something else: more efficient remanufacturing.
What is remanufacturing?
Remanufacturing is an industrial process where used, perhaps damaged or broken products or components are restored to a like new, or better than new state where they can then begin an entirely new lifecycle. Importantly, this must happen in a controlled and repeatable, environmentally friendly way.
What separates remanufacturing from other similar concepts like recycling and refurbishment is the idea of it being an industrialised process and the phrase “like new or better”. Remanufacturing sits right at the heart of the ideal circular economy.
To get a clear understanding of the principles of remanufacturing, it’s helpful to look at each stage of the product lifecycle compared to the equivalent stage in remanufacturing.
Remanufacturing is significantly different to recycling and refurbishment. Remanufacturing typically means disassembly, cleaning and repair, inspection and verification of specified characteristics then reassembling the item returning it to its original state (or better – eg, upgraded). Recycling goes beyond disassembly. It completely breaks down a product, separating out different materials which we can then use to create new products. The recycling process, stripping a product down to its base materials, often causes a degradation of the original material which limits the number of times it can be recycled for the same purpose. Remanufacturing is a less intrusive process, consequently, it normally creates better products and uses less energy.
However, for all its benefits, there is still a problem: efficiency. The costs and the complexity of remanufacturing an item are holding back widespread adoption. To understand how and why that is, we need a breakdown of the generalised process.
From manufacturing to remanufacturing – a comparison of lifecycle stages
Manufacturing lifecycle | Remanufacturing lifecycle | ||
---|---|---|---|
Design | Creating the product’s blueprint to fulfill customer requirements in terms of fit, form and function. Up to 80% of a product’s environmental impacts are locked in at this stage. | Assessment | Similar to the design stage in traditional manufacturing, a product’s function, value, and condition are evaluated. This determines how it to disassemble and remanufacture an item. |
Production | Building the product, generally on a large scale in an assembly line product facility. | Restoration and reconstruction | This parallels the production phase of traditional manufacturing. Instead of creating new products, we clean, repair, and refurbish existing components. |
Usage | Stage remains the same in both cycles. | Usage | Stage remains the same in both cycles. |
End of life | Disposal, recycling, refurbishment, repurposing, and the entrance point into remanufacturing. | Sustainability | Instead of disposal, the product or its components reenter the cycle, reducing waste and the need for raw materials. |
In the manufacturing cycle, design intent is the driving force and the determiner of all the subsequent processes. In the remanufacturing cycle, the same is true for the assessment stage. This is the key to creating a more efficient remanufacturing process.
Instead of receiving a quantity of used products to go into a remanufacturing assessment process, imagine if we already knew the condition every component of product. Items could be immediately sorted, inspected and directed to the next stage of the process with the equipment ready to jump into action as soon as the object is in place.
Digital transformation of remanufacturing
At its core, digital transformation is about putting the right information in the hands of the right people, wherever they are in the world. If we apply that idea to remanufacturing, we end up with a vastly more efficient assessment phase of the remanufacturing cycle.
A 2022 research paper from academics at the University of Coventry (available online here) makes a number of useful observations. Deploying technologies like IIoT (Industrial Internet of Things), RFID (Radio Frequency Identification), Big Data Analytics, Collaborative Robots and Data-Driven simulations in the initial manufacturing process, remanufacturers can leverage a wealth of information to streamline their operations. Processes that were once subject to high levels of uncertainty suddenly become clearer and more predictable.
They would be able track and trace products and resources throughout the entire supply chain. When a product arrives at the remanufacturing facility, the organisation would already have a clear idea of the specific processes required for each component.
Remanufacturing intelligence: A vision of the future
If we allow our imaginations to run away with us for a moment, an exciting vision of the future begins to appear.
Perhaps, in the future, manufacturers will have “remanufacturing lines” running alongside their initial production lines. Products return to the facility and enter the remanufacturing line where AI systems recognise the part and instigate autonomous disassembly processes. With a combination of dynamic milling on welded joints followed by additive manufacturing to patch and repair flaws, components could arrive at a like-new state. From there, robot arms reach in and transpose the component directly into a new product.
With advanced analytics, the organisation could go beyond identifying and sorting products. They could develop flexible remanufacturing facilities that accommodate a range of product lines, dynamically responding to changes in supply and demand. The big challenge is that any number of components could re-enter the cycle at the same time. If we take a car for example, the axle is usually at a very different point in time to the alternator.
Organisations would need a really effective, digitally driven operation at the goods-in stage. It would be like that of a logistics company today being able to take in a range of different goods, each with different dimensions, values and handling requirements. The remanufacturing goods-in process would need to combine advanced analytics with AI and robotics to identify and sort the returning products. It should also prioritise them based on condition, the demand and where they will fit into the ongoing production line.
One of the critical points for the future of remanufacturing will be managing shared responsibility among manufacturers, remanufacturers, consumers and authorities. The information circulation and product traceability required for efficient remanufacturing will mean much closer collaboration between stakeholders. Overcoming this will help drive innovation and spur on the drive for ever more sustainable production methods.
And now we want to hear from you. Do you agree with us? What are your thoughts on the future of manufacturing? Share this blog with your networks and join the conversation online.
For quality that touches peoples lives
Hexagon’s Manufacturing Intelligence blog is your go-to source for the latest manufacturing thinking. From expert commentary to industry perspectives, it’s designed to empower leaders and professionals to make smarter decisions, drive innovation and turn ideas into impact.