Real-time design and feedback of 3D-printed orthopaedic insoles
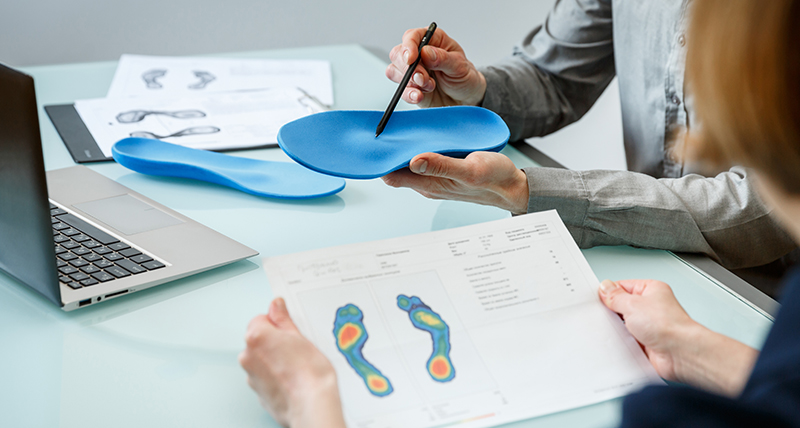
Back pain, foot and lower limb problems, and overpronation, orthopaedic insoles improve and correct a variety of mobility problems. According to one estimate, the global market will be worth over USD 5bn by 2027. This growth is a result of many converging areas of research. That’s things like our understanding of sports injuries, new materials like thermoplastics which simplify the production process, and now the digital transformation.
Read on to find out more and hear directly from the research team in France pushing this sector to the next level in an exclusive video presentation for Hexagon.
Until a few years ago, if you needed orthopaedic insoles, the process might have taken weeks or even months. A podiatrist would make an impression of your feet with a plaster cast which could then take 24 hours to harden. That impression would then be sent to a laboratory where it would be used, along with instructions and measurements from the podiatrist, to create a custom insole for each individual. It was a lengthy process resulting in an expensive product. The only way to test these insoles was for the patient to try them out for a few days, at which point it would be too late to make any adjustments.
Nowadays podiatrists use memory foam and thermoplastics to create a custom insole in a matter of minutes but that only solves half the problem. The patient still performs the final testing at home and returns to the doctor if the problem persists.
In the medical sector, the term ‘digital twin’ takes on a very literal meaning
That was the situation before the experts over at the Laboratoire de Biomécanique Appliquée (The Laboratory of Applied Biomechanics) in Marseille, France, took up the challenge. In the medical sector, the term ‘digital twin’ takes on a very literal meaning. Researchers at the Laboratory of Applied Biomechanics create virtual humans which are then used in diverse areas like the study and prevention of trauma, advanced diagnosis or developing new surgical techniques.
With 3D simulations and digital twin technology, the team creates comprehensive models of a patient’s feet and lower limbs. These models are detailed in a way that far exceeds a simple impression taken with memory foam. They include the underlying bone structure, the soft plantar tissue, skin, ligaments, the flexibility and location of joints, even the nature of the ground underneath the foot.
The digital twin accounts for all the factors simultaneously and can show them working together in motion. It creates a comprehensive model of a person’s walking gait. A podiatrist can then use this model to create and modify a virtual insole, observing the effects in real time for rapid optimisation. Podiatrists can see the pressure distribution of the foot as the patient moves and modify the insole accordingly long before a physical model is produced. A process that used to take weeks, or even months, now happens in a matter of minutes.
Hear directly from Michel Behr, Deputy Head of the Research Department at the Laboratoire de Biomécanique Appliquée, as he discusses the project in this exclusive presentation for Hexagon:
https://events.hexagon.com/hxgnlive-designandengineering/agenda/session/579272
For quality that touches peoples lives
Hexagon’s Manufacturing Intelligence blog is your go-to source for the latest manufacturing thinking. From expert commentary to industry perspectives, it’s designed to empower leaders and professionals to make smarter decisions, drive innovation and turn ideas into impact.