Optimising gearboxes with AI and machine learning
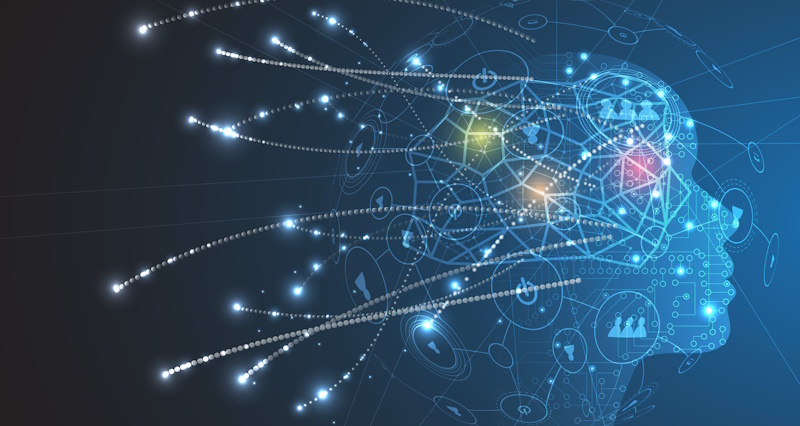
Imagine a car was like a human body. The engine is like the heart, keeping everything going with a heartbeat like the revolutions of the motor. The steering system is like the brain guiding the course of the vehicle. The chassis is the skeleton.
Cars can’t run without fuel, neither can a human being live without food. The exhaust is like the digestive system. Oil, like blood. The electronics are comparable to the central nervous system.
And the transmission? The gearbox? Like the muscles. They turn the power of the engine into motion. Without effective muscles, a human being is unable to move, unable to sustain the basic spark of life.
So it is with a vehicle. The analogy works very well. It goes beyond power conversion because muscles also work together to amplify a force much like gears in a transmission system. They also ensure a certain coordination of action and smoothness of motion.
Biologists tell us that the muscles in the human body are the result of around 600 million years of evolution.
What if, with artificial intelligence and machine learning, those 600 million years could be condensed into a few minutes? All those innumerable variations and iterations, invented and tested at the click of a button? It would be survival of the fittest with zero cost.
Leveraging AI and machine learning for component analysis
AI optimises the design process by enabling a more robust analysis of variables and their impact. By running strategic mechanism analyses, like Design of Experiments (DOE), AI can generate a data matrix that predicts the results for new design variables and it will learn from the data, allowing for more accurate and efficient predictions in future.
Enhancing functional responses with machine learning
Machine learning (ML) is a subset of AI that can analyse design variables and optimise the interaction between different components. Using potentially limitless virtual prototypes, ML will identify the sensitivity of tolerance ranges for each component. This makes it possible to predict the response for new tolerance ranges accordingly and iterations using ML require much less time compared to traditional methods.
Optimal functionality and reduced manufacturing cost
The benefits of artificial intelligence and machine learning go way beyond technical improvements. This strategy can lead to substantial cost savings in manufacturing. When tolerance ranges that minimally influence the response are increased, and those that affect the mechanism functionality are decreased, the overall manufacturing cost can be significantly reduced.
This optimisation not only ensures top functionality for the vehicle but also contributes to a more efficient production process. To explore the deep impact of AI and ML in optimising gearbox mechanisms, we conducted a detailed case study. Uncover how AI and ML are revolutionizing manufacturing by downloading our full case study here.
We invite you to enhance your understanding by registering for our 5-part webinar series “Navigating the AI/ML Landscape in Modern Engineering. Let us navigate this journey together, opening doors to innovation and efficiency with ODYSSEE.
For quality that touches peoples lives
Hexagon’s Manufacturing Intelligence blog is your go-to source for the latest manufacturing thinking. From expert commentary to industry perspectives, it’s designed to empower leaders and professionals to make smarter decisions, drive innovation and turn ideas into impact.