Connected quality: Getting the basics in place
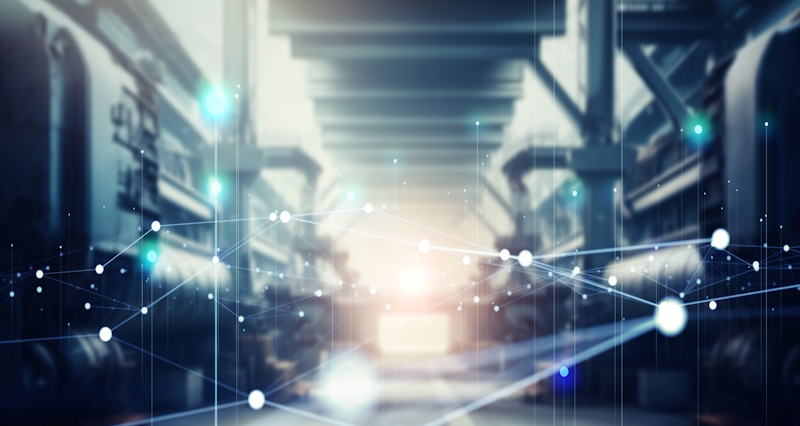
Connected quality goes beyond point solutions. It integrates systems and processes to deliver continuous improvement across the organisation.
To some, it might sound straightforward. To others, it could seem like a daunting prospect. A connected, holistic approach to quality is perhaps the biggest opportunity to win an advantage over your competitors. We need to make sure we have the right data, in the correct context, shared with the right people in a timely fashion. Without data we are just guessing, stumbling around in the dark. Data is like vision. Without it we are blind.
We can improve things without measuring them – we just won’t be able to see and act on it. But it’s also possible to damage things without measuring them too, and again, you won’t be able to understand the consequences until it’s happened.
In any situation, how do we know the best course of action? If your business is successful, how do we ensure that success continues? When things go wrong, how do we know what corrective measures to take?
It’s only when we have the right data that we can formulate the best quality management strategies from scheduled maintenance to quality control and process improvements. Data provides clarity and when combined with context and experience, data converts to information and knowledge. This is where insight can facilitate change and inform our plans for growth and development.
By combining real-time insights from across the product lifecycle and the manufacturing value chain, we can create a circular process that prioritises connected quality through every stage. More than this, it unlocks multiplier gains – from concept to customer.
Creating a digital thread for connected quality
Generating data is not a problem. To transform impactfully and gain new capabilities, we need to connect our disparate systems, unite data in one place and put it to work.
This is vital because quality is a result of connectivity. Quality only becomes a scalable result when every sensor, every piece of software in your facility is connected. With data as the connecting thread, quality is woven into the fabric of your enterprise spanning everything from products and production to planning and procurement.
Right now, the application of big data for enhancing quality is seriously lacking and fragmented. This is a problem because it obstructs our ability to leverage AI to transform datasets from event-driven to predictive. By setting dimensional quality triggers we can pre-empt quality incidents.
Creating a quality digital thread that connects your systems linking technology across your facilities for full enterprise alignment, means that data can be centralised, mined for generative improvements and acted on. With no need to rip and replace technology, you can maximise existing infrastructure investment.
AI/ML contextualisation of data allows you to make step changes to your business while embedding continuous improvement. Co-pilot assistance gives you the freedom you need to advance towards a long-term vision where high-fidelity data sets are harnessed for full automation.
The structuring and accessibility of relational data is critical. Designing a quality-centric data mart from the ground up that acts as both a system of record (as a single source of truth) and a system of engagement throughout the enterprise, will provide the versatility needed to meet various stakeholder needs.
Developing a technology plan around the single, connected quality digital thread will help you structure, mine and leverage data with generative tools to give you game-changing capabilities.
Sources of quality data across the value chain
Business function | Data sources |
Inbound logistics | Freight and shipping data, inventory management systems, purchasing data, supplier surveys and scorecards |
Manufacturing | Production data, conformance, machine or equipment data, employee performance metrics, material usage data, process control |
Outbound logistics | Delivery performance data, transport management data, customer surveys, return and refund rate, warehouse/inventory management, point of sale data |
Sales and marketing | Customer relationship management, marketing automation tools, web analytics, social media engagement, sales data, customer feedback, market research |
Aftersales service | Direct customer feedback, average resolution time, first response resolution, volume of support issues, type and severity of support issues |
Management | Strategic planning data, business goals and objectives, financial data systems, systems performance, project management tools, business intelligence tools |
Human resources | Human resource information systems, employee performance data, employee engagement, learning management systems, attendance and absenteeism, employee recognition platforms |
Research and development | Monitor patent databases to ensure uniqueness and quality of output, contribution to financial performance, market research data, benchmarking |
Purchasing | Market trends and pricing data, supplier quality/reliability data, procurement software data, inventory data, purchase orders, contracts, financial data |
The power of a collaborative approach
Quality is a team game. We work better when we work together. Hexagon’s Advanced Manufacturing Report highlights that 88% of manufacturers think improving communication would improve product quality.
When you see a typical company value chain, you begin to see where dependencies exist and how collaboration between departments can boost quality within an organisation.
If you think of a business as a linear sequence of actions that result in a finished product going to a customer, you end up with a problem. The points at distinct ends of that line are quite far removed from each other. You might think that goods inwards or procurement and after sales service are far removed from each other, but quality data from one area of business can and should be used to inform activities elsewhere. This is the essence of connected quality.
A collaborative approach to data sharing is just one element of a much broader idea. The power of collaboration means bringing in a multiplicity of people with different viewpoints, each looking at the same problem from a different angle.
We don’t need to look very far before we find examples of how this approach could work: Design and Production teams might work together to resolve design flaws impacting manufacturing efficiency. Supply chain and production teams might collaborate to address supplier issues impacting product quality.
A truly collaborative approach facilitates much faster problem solving. It promotes a culture of shared responsibility for quality throughout the organisation and it leads to innovative solutions that individual departments might not arrive at alone.
Connected quality: Bridging the gap between data and collaboration
Industry commentators are describing data as a language that facilitates collaboration among different departments. Accurate data gives us an unbiased viewpoint of every part of an organisation. It spans the entire value chain and beyond into the wider industry sector, geographical region – even to a global perspective.
Data provides the facts, but facts need interpretation. Observations need context. Insights need application.
One way to ensure this happens is by creating a data-driven culture, one that democratises information. The journey towards digital transformation must involve everyone making data accessible and interpretable for every department. Access on its own is not enough, to promote collaboration there needs to be a shared oversight, understanding and responsibility.
This will create an incentive to go further and deeper. Be curious and search for the insights that data can reveal.
This blog first appeared as part of our Quality ebook. Quality is the biggest needle mover in our sector, download the full report and start your transformation.
For quality that touches peoples lives
Hexagon’s Manufacturing Intelligence blog is your go-to source for the latest manufacturing thinking. From expert commentary to industry perspectives, it’s designed to empower leaders and professionals to make smarter decisions, drive innovation and turn ideas into impact.