In recent years, the idea of anti-fragility has gained popularity in numerous fields from finance to healthcare – but what does it mean in a manufacturing context? What are the key principles and how can it take manufacturing to the next level?
Let’s start with anti-fragility. Quite simply, this is the idea that systems, just like nature and evolution, adapt and strengthen when subjected to stressors. Every problem that is solved, every weakness removed, becomes a strength that helps to guarantee future survival.
Anti-fragility is an attribute that improves the self-organising capabilities of a system, allowing living systems to react to external shocks. Thus, an anti-fragile strategy places more effort on reducing internal vulnerabilities than on the search for optimal or excellent solutions.
As a sector that undergoes constant innovation, it is ironic perhaps that our sector’s vulnerability – something stopping us from getting stronger – is the success of our past innovation.
Fragile manufacturing – analog, rigid, repeatable
When it comes to factory size, layout, configuration, process, tooling and machine specification – much of what we see in manufacturing is built on 100-plus-year-old analog systems.
In the early industrial revolution, we mastered the art of scaling and repetition. Entire factories would be built and configured to specialise in producing just one thing. But this isn’t just a historic production template.
As the term giga-factory reminds us, even the most cutting-edge production facilities are built at scale to make very specific lines of parts and products. All machinery is procured and configured to meet that one purpose. The whole line is precisely calibrated to achieve optimum output.
This has never been a problem in the past because the pace of change was steady. In the era of digitalisation and disruption – the pace of change, however, will be dizzying.
What is an anti-fragile factory?
Unlike the production model we all know, an anti-fragile factory is designed to thrive in uncertain environments. With resilience built into the system, it can embrace change and use it to improve.
The anti-fragile manufacturing model depends on two things. First, the entire end-to-end manufacturing process must be digitalised from design to inspection enabling the creation of an information system with a feedback loop. Second, production cells harnessing the very latest technology are used to ensure a high degree of flexibility. Incumbent cells can be augmented through advanced process simulation and the introduction of more automation and new tooling that enables greater flexibility. By learning from real-time process information and adapting, the system constantly iterates toward ultimate efficiency. These cells can also benefit from the addition of 3D printing technologies, which can free up production machines and aid in faster job setup through more dynamic methods of fixture and jig creation.
Greenfield projects can be even more rewarding. Where cells are configured to leverage the ultimate flexibility that 3D printing and automation provide for production capabilities, the results can be truly incredible. The system can design and print any required structure and move seamlessly between tasks, designs and applications with no tooling, no fixturing and no reconfiguration of the hardware. The data overlay means it is flexible, adaptable and able to respond quickly to feedback as well as changes in demand, disruptions in supply chains, or unexpected events.
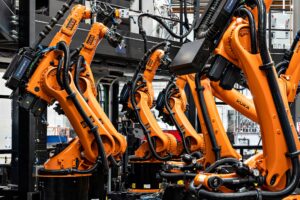
Caption: An anti-fragile production cell as pioneered by Divergent. The Divergent Adaptive Production System (DAPS) is a complete modular digital factory for complex structures.
En-masse, anti-fragile production makes it possible to print any structure anywhere in the world at the press of a button. The cells can switch from printing anything such as automotive parts to a drone structure, making it as easy as hitting Ctrl+P on your computer.
Rather than changing the machine to make the product, you’re adapting the production process to allow flexibility by harnessing the latest additive, subtractive and automated technologies. It is a model that is resilient enough to cope with anything you throw at it.
How anti-fragile production can drive innovation
Flexible or anti-fragile manufacturing will not only change how we make things – it will fuel innovation and invention, entirely reshaping the product landscape by providing a platform to try out new ideas quickly.
A major factor here is that it will democratise manufacturing. People with bold ideas for new products with the potential to disrupt a sector will be able to bring them to market more easily than ever before as the Factory as a Service (FaaS) model, which hinges on the anti-fragile process, matures.
Another driver will be the exponential increase in the rates of iteration. In this case, autonomous technologies will be able to observe product performance data without the pre-judgement of people – suggesting radical redesigns to help optimise performance. Here technology will propel human ingenuity by opening entirely new avenues for inventors and designers to explore.
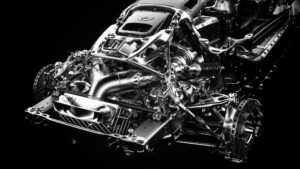
Caption: A 3D-printed hypercar structure from Czinger Vehicles.
The shoots of this change are already visible, perhaps most so in the automotive world where we’re already seeing generatively designed innovation combining multiple parts into one housing that is lighter in weight, has fewer weak points and offers improved performance.
We can expect this kind of leap in innovation to spread throughout manufacturing.
Building anti-fragile capabilities
If all of this sounds distant and daunting, rest assured that the shift to anti-fragility can be incremental. Anti-fragile techniques like additive manufacturing and generative design can and must work in synergy with traditional methods.
Additive manufacturing gives firms rapid prototyping and customisation abilities, while subtractive techniques are used for precision machining and finishing additive parts. Subtractive manufacturing excels at achieving precise dimensions and surface finishes. This combination of techniques allows the anti-fragile factory to tackle a broader range of manufacturing requirements and cater to diverse customer demands.
To help you work towards anti-fragility, no matter where your factory stands on the transformation pathway, the following two stepping stones are essential:
- Automation – by equipping your facility with automation hardware and software, you are not only investing in assets that increase productivity and output – you are digitising your operations. The more you digitise your end-to-end process, the closer you will be to achieving anti-fragility. Automation brings new levels of accuracy and opportunity to production methods such as subtractive manufacturing. And the data that you add to the manufacturing picture will help you to further optimise production while pushing innovation in product development.
- 3D printing – even viewed as a standalone, additive manufacturing is transformative. Investing in the technology, even if it’s just for prototyping will bring huge benefits to your business. Doing this is also a stepping-stone to use in production. Most of all though, additive brings new levels of flexibility to production. It gives you the agility you need to change and adapt quickly. Once you start harnessing the technology, you begin to see more and more uses for it in production. And when it is properly embedded in production, it will help you to harness data, meaning you can iterate and innovate like never before.
Reducing business risk with anti-fragile manufacturing
When you need to quickly re-evaluate and innovate to stay ahead of the change curve, the last thing you need is a rigid, analog factory that is heavily customised to produce current offerings.
At the very least, rigid processes mean there are major cost implications to shifting production. Some rigidly specified facilities could even become obsolete as the ability to redesign and re-equip an entire factory is outstripped by the pace of change.
The flipside of risk is opportunity. With a new idea, revolutionary new products could enter production in record time. Entire production models could be refocussed to meet market needs. It even becomes entirely possible for manufacturers to enter new verticals overnight.
In times of innovation, democratisation and disruption – entire industries and major organisations will need to turn on the head of a pin quickly making anti-fragility critical to the long-term commercial outlook of manufacturing businesses.
Anti-fragile production can empower sustainable manufacturing
Anti-fragile manufacturing will do more than push the boundaries of what is real – it will help manufacturing become more sustainable.
Additive manufacturing is continually advancing. Automation too is helping to transform CNC machining and other subtractive manufacturing methods by further digitising production and optimising material usage. Combine advancing technology with materials innovation and our sector is fast adding viability to the circular economy model.
Thanks to powerful design tools, we will use fewer raw materials to manufacture stronger, better-performing goods than ever before. And by harnessing data to its full potential – parts and products will last longer and be more serviceable, meaning that products will stay in use for much longer.
More than this though is the potential to localise production. With shipping and transport mileage detrimental to a product’s environmental performance, producers can make and sell locally, slashing their carbon footprint by manufacturing in several carefully chosen global locations.
The 6 key features of anti-fragile manufacturing
- Redundancy: With redundancy built into its systems, there are backup plans in place in case of disruptions. For example, there may be multiple suppliers for critical components, or there may be extra inventory on hand to cover short-term supply chain disruptions.
- Modularity: Systems are designed to be easily reconfigured or repurposed as needed. For example, production lines can be quickly retooled to produce different products or entire factories can be repurposed to produce entirely different goods.
- Flexibility: Able to adjust production levels quickly to meet changing demand; the factory can ramp up production to meet a sudden increase in orders or scale back production during a period of slow demand.
- Agility: Decision-making processes that allow for quick responses to changing circumstances. This may mean empowering employees to make decisions on the spot or implementing rapid response teams to deal with unexpected events.
- Continuous Improvement: Improvement that uses data and feedback to identify areas for optimisation and refinement, implementing new technologies, streamlining processes, or investing in employee training and development.
Don’t just survive – thrive
The benefits of anti-fragility are clear – building resilience and flexibility into systems allows companies to reduce their exposure to risk and increase their ability to adapt to changing circumstances. This in turn can lead to increased productivity, improved customer satisfaction and, ultimately, a more sustainable business model.
Businesses that begin digitalising and experimenting with flexible production technology, have the perfect opportunity to prioritise innovation and see where it takes them. By embracing change and building resilience into systems, anything is possible.
Connect with Jason Walker on LinkedIn to collaborate and work towards a sustainable future for manufacturing.